OEM manufacturer Cl300 Pipe Flange - Forged Bars – DHDZ
OEM manufacturer Cl300 Pipe Flange - Forged Bars – DHDZ Detail:
Open Die Forgings Manufacturer In China
Forged Bars
Common used material: 1045 | 4130 | 4140 | 4340 | 5120 | 8620 | 42CrMo4 | 1.7225 | 34CrAlNi7 | S355J2 | 30NiCrMo12 |22NiCrMoV12
FORGED BAR SHAPES
Round bars, Square bars, Flat bars and Hex bars. All Metals has the forging capabilities to produce bars from the following alloy types:
● Alloy steel
● Carbon steel
● Stainless steel
FORGED BAR CAPABILITIES
ALLOY
MAX WIDTH
MAX WEIGHT
Carbon, Alloy
1500mm
26000 kgs
Stainless Steel
800mm
20000 kgs
FORGED BAR CAPABILITIES
The maximum length for forged round bars and hex bars is 5000 mm, with a maximum weight of 20000 kgs.
The maximum length and width for flat bars and square bars is 1500mm, with a maximum weight of 26000 kgs.
A forged bar or a rolled bar is produced by taking an ingot and forging it down to size by, generally, two opposing flat dies. Forged metals tend to be stronger, harder and more durable than cast forms or machined parts. You can get a wrought grain structure throughout all sections of the forgings, increasing parts ablitity to withstand warping and wearing.
Shanxi DongHuang Wind Power Flange Manufacturing Co., LTD., as an ISO registered certified forging manufacturer, guarantee that the forgings and/or bars are homogenous in quality and free of anomalies which are detrimental to the mechanical properties or machining properies of the material.
Case:
Steel Grade EN 1.4923 X22CrMoV12-1
Structure Martensitic
Chemical composition % of steel X22CrMoV12-1 (1.4923): EN 10302-2008 |
||||||||
C |
Si |
Mn |
Ni |
P |
S |
Cr |
Mo |
V |
0.18 - 0.24 |
max 0.5 |
0.4 - 0.9 |
0.3 - 0.8 |
max 0.025 |
max 0.015 |
11 - 12.5 |
0.8 - 1.2 |
0.25 - 0.35 |
Applications
Powerplant, Machine engineering, Power generation.
Components for pipe-lines, steam boilers and turbines.
Delivery form
Round bar, Rolled Forgings Rings, Bored roundbars, X22CrMoV12-1 Forged bar
Size: φ58x 536L mm.
Forging (Hot Work ) Practice
Materials are loaded in furnace and heated. When the temperture reaches 1100℃, metal will be forged. It refers to any mechanical process that shapes metal ulilizing one or more dies, e.g. open/closed die forging, extrusion, rolling, etc. During this process, the temperture of metal falls. When it decreases to 850℃, metal will be heated again. Then repeat hot work at that elevated temperature(1100℃). The minimum ratio for hot work ratio from ingot to billet is 3 to 1.
Heat Treatment Procedure
Load the preheat treat machining material into heat treatment furance. Heat to temperature of 900 ℃. Hold at temp for 6 hours 5 minutes. Oil quench and temper at 640℃.Then Air-cool.
Mechanical properties of X22CrMoV12-1 forged bar (1.4923).
Rm - Tensile strength (MPa) (+QT) |
890 |
Rp0.2 0.2% proof strength (MPa) (+QT) |
769 |
KV - Impact energy (J) (+QT) |
-60° 139 |
A - Min. elongation at fracture (%) (+QT) |
21 |
Brinell hardness (HBW): (+A) | 298 |
Any material grades, other than above mentioned, can be forged as per the customer's requirement.
Product detail pictures:
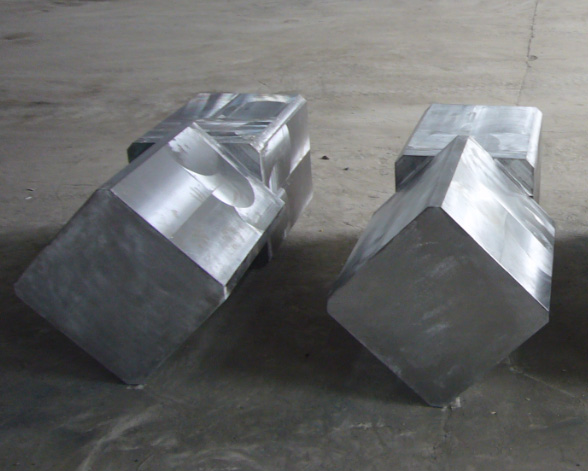
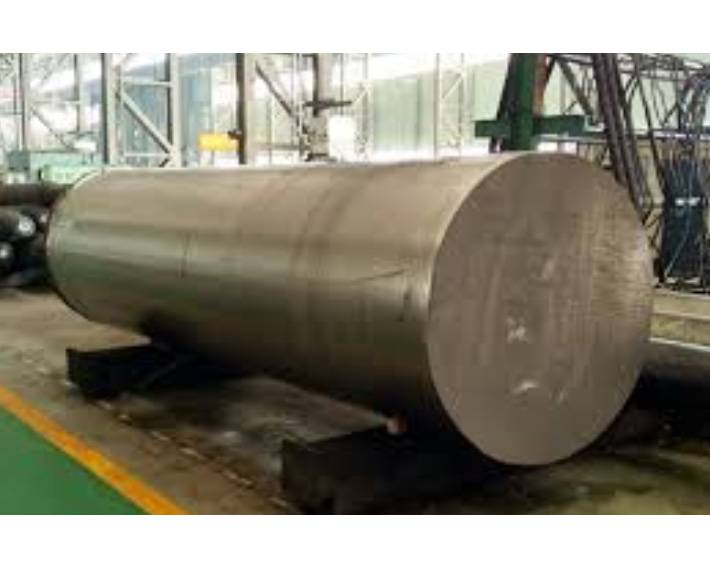
Related Product Guide:
We constantly believe that one's character decides products' high quality, the details decides products' high-quality ,together with the REALISTIC,EFFICIENT AND INNOVATIVE crew spirit for OEM manufacturer Cl300 Pipe Flange - Forged Bars – DHDZ , The product will supply to all over the world, such as: Cairo, Jamaica, Uruguay, Our production have been exported to more than 30 countries and regions as first hand source with lowest price. We sincerely welcome customers from both at home and abroad to come to negotiate business with us.

Reasonable price, good attitude of consultation, finally we achieve a win-win situation,a happy cooperation!
